Choose aluminum for non-magnetic applications
The unsung hero for non-magnetic vacuum applications, aluminum is lightweight, offers superior UHV characteristics, and is easy to machine, making it an ideal material for demanding requirements in science and industry.
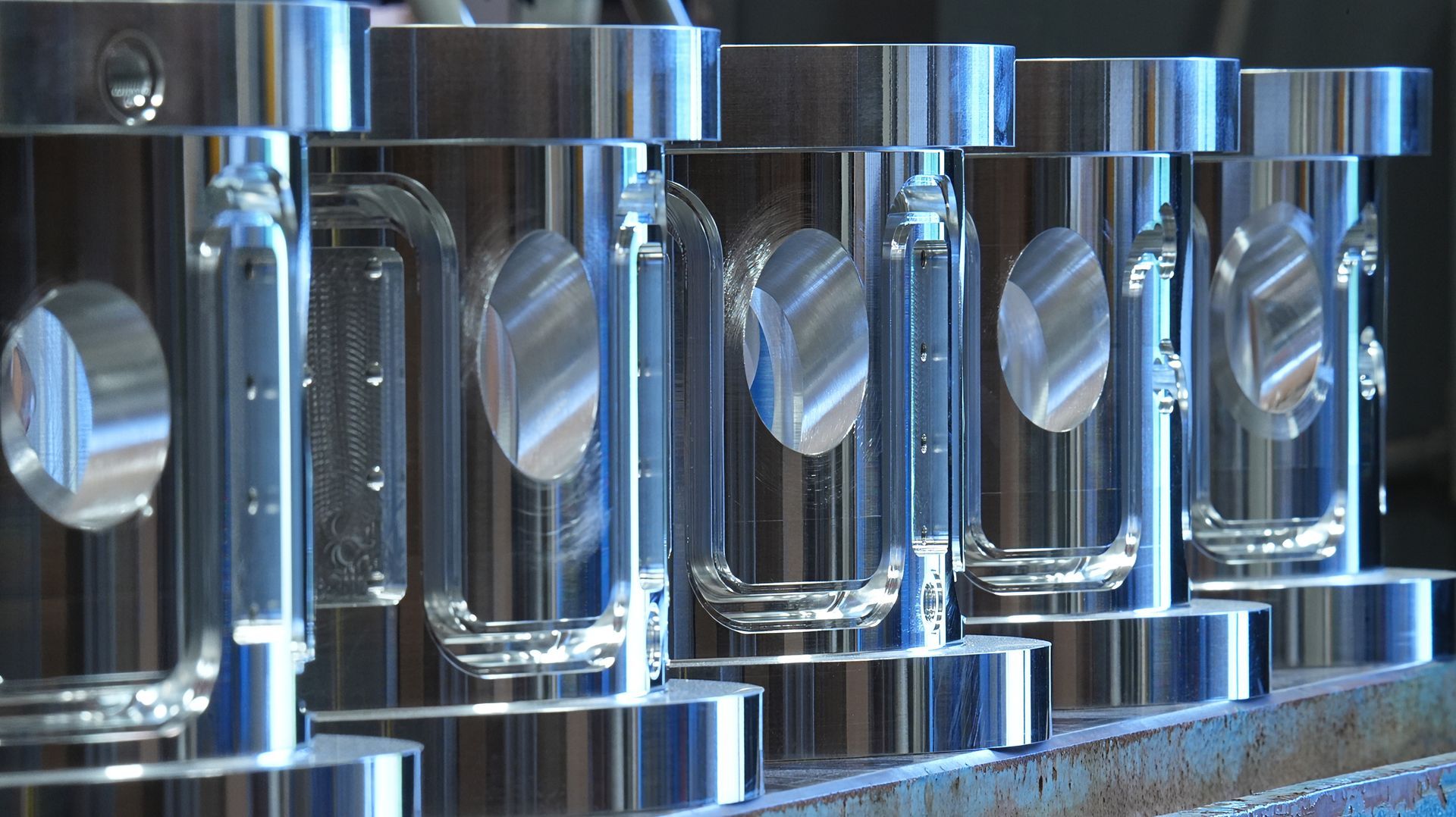
lower magnetic permeability
In contrast to stainless steel, aluminum’s significantly lower magnetic permeability is especially well suited for semiconductor manufacturing, aerospace, precision metrology, and scientific research – all of which require vacuum systems with minimal magnetic interference.
Classified as a paramagnetic material, aluminum does not exhibit ferromagnetism like iron, nickel, or cobalt. And when exposed to an external magnetic field, aluminum incurs limited magnetization. Unlike ferromagnetic materials, which retain magnetization even after the removal of an external magnetic field, aluminum’s magnetization disappears almost instantly once the external field is removed. The weak paramagnetic response of aluminum is due to its electronic structure. The material lacks unpaired electrons in its atomic orbitals, which are necessary for strong magnetic interactions.
Aluminum Versus Stainless Steel
Magnetic permeability (μ) is a measure of a material's ability to form a magnetic field within itself, indicating the ease with which a material can be magnetized. It is expressed relative to the permeability of free space (μ0), known as relative permeability (μr).
- Aluminum has a relative permeability very close to 1 (μr 1.000022), meaning it behaves nearly the same as free space and does not significantly distort or concentrate magnetic fields.
- Austenitic stainless steels (such as 304 and 316 SS) have a relative permeability μr of 1.003 and 1.05 when fully annealed but may exhibit weak magnetism due to cold working (machining) and may also contain ferritic patches which have extraordinarily high permeabilities, particularly in welds.
- Ferritic and martensitic stainless steels (such as 410 and 430 SS) are magnetic with significantly higher permeability values, typically μr above 100.
Even in applications that don’t require extraordinarily low magnetic permeabilities, aluminum is often a more practical choice because its permeability is not changed during machining and welding operations. Austenitic stainless steels have a crystal structure that can be disturbed by machining, forming or welding, causing the structure to become martensitic in nature.
The martensitic form of stainless steel is ferromagnetic and can have a magnetic permeability in the range of µr ~1.5–10+. The paramagnetic properties of stainless can often be restored by annealing. However, the high temperature process can affect the dimensional stability and accuracy of machined features.
Compared to stainless steel, especially the martensitic grades, aluminum exhibits limited interaction with magnetic fields. By understanding the differences in magnetic properties between aluminum and stainless steel, engineers and designers can make informed choices for material selection in critical applications.
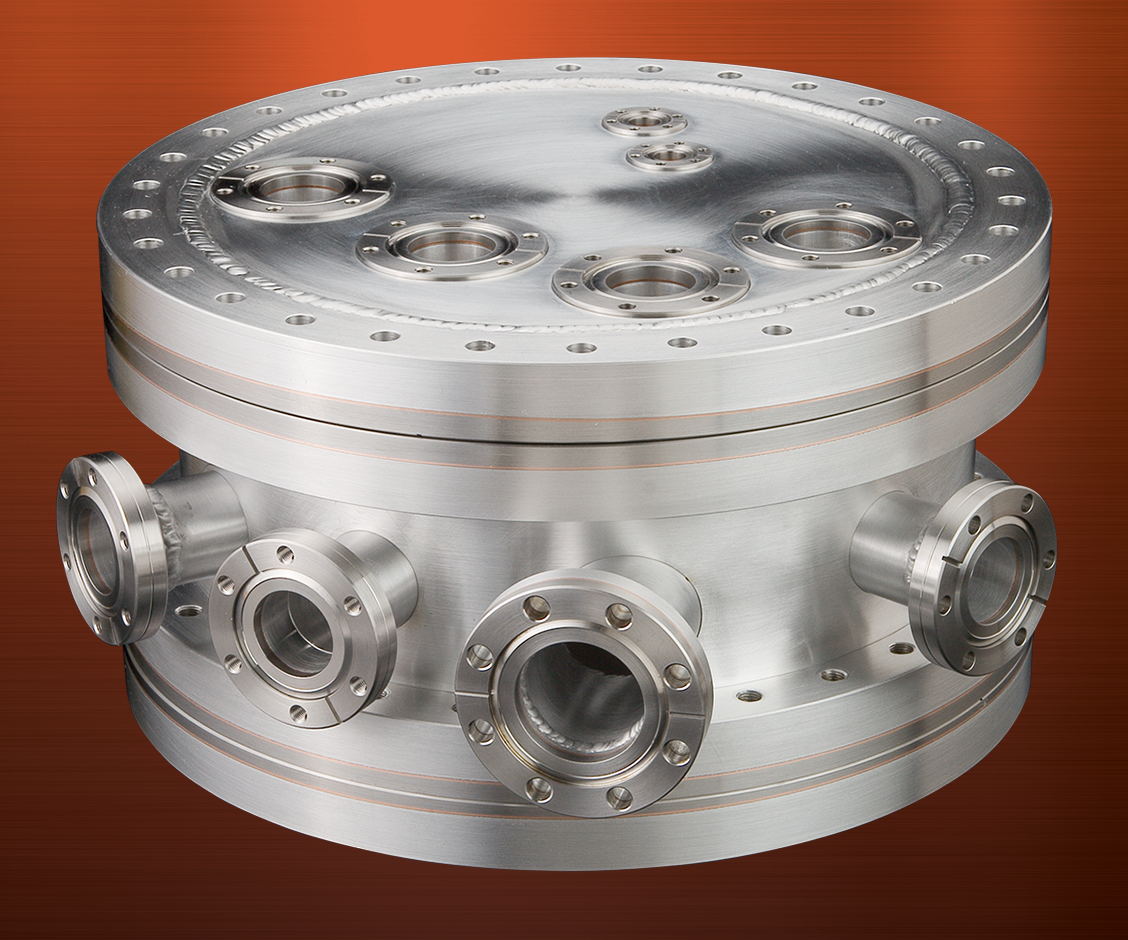
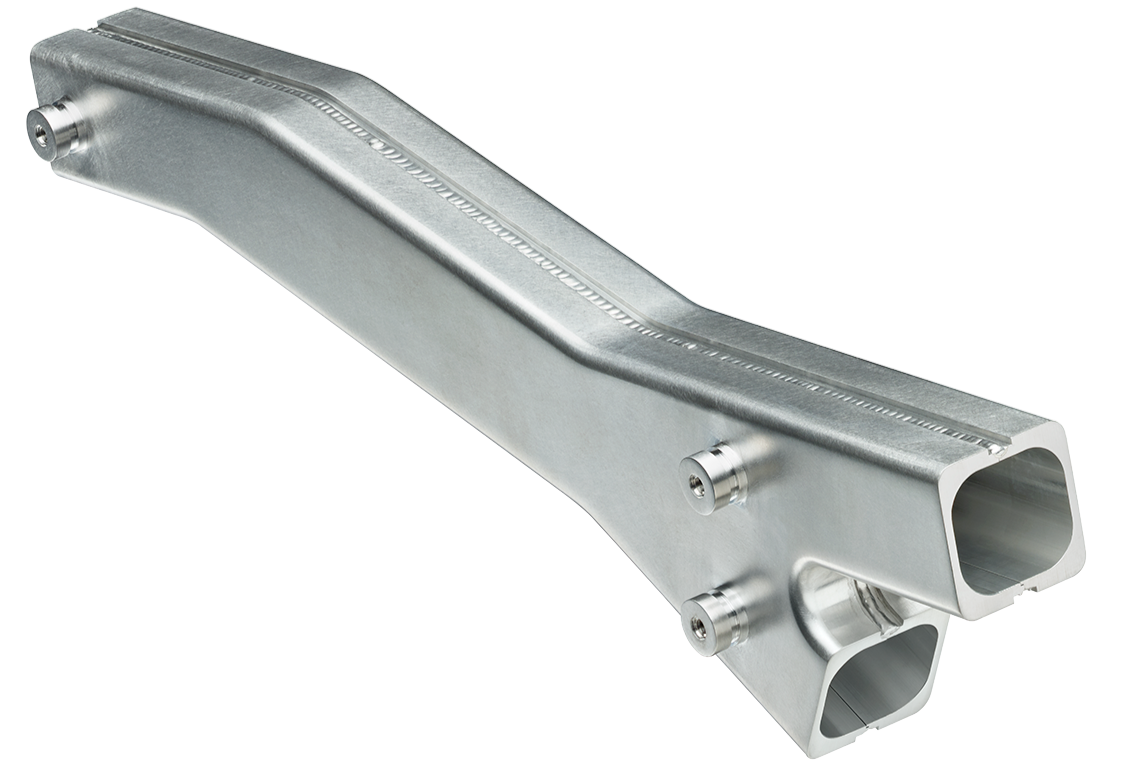
Compared to stainless steel, especially the martensitic grades, aluminum exhibits limited interaction with magnetic fields making it an ideal vacuum material for critical applications.
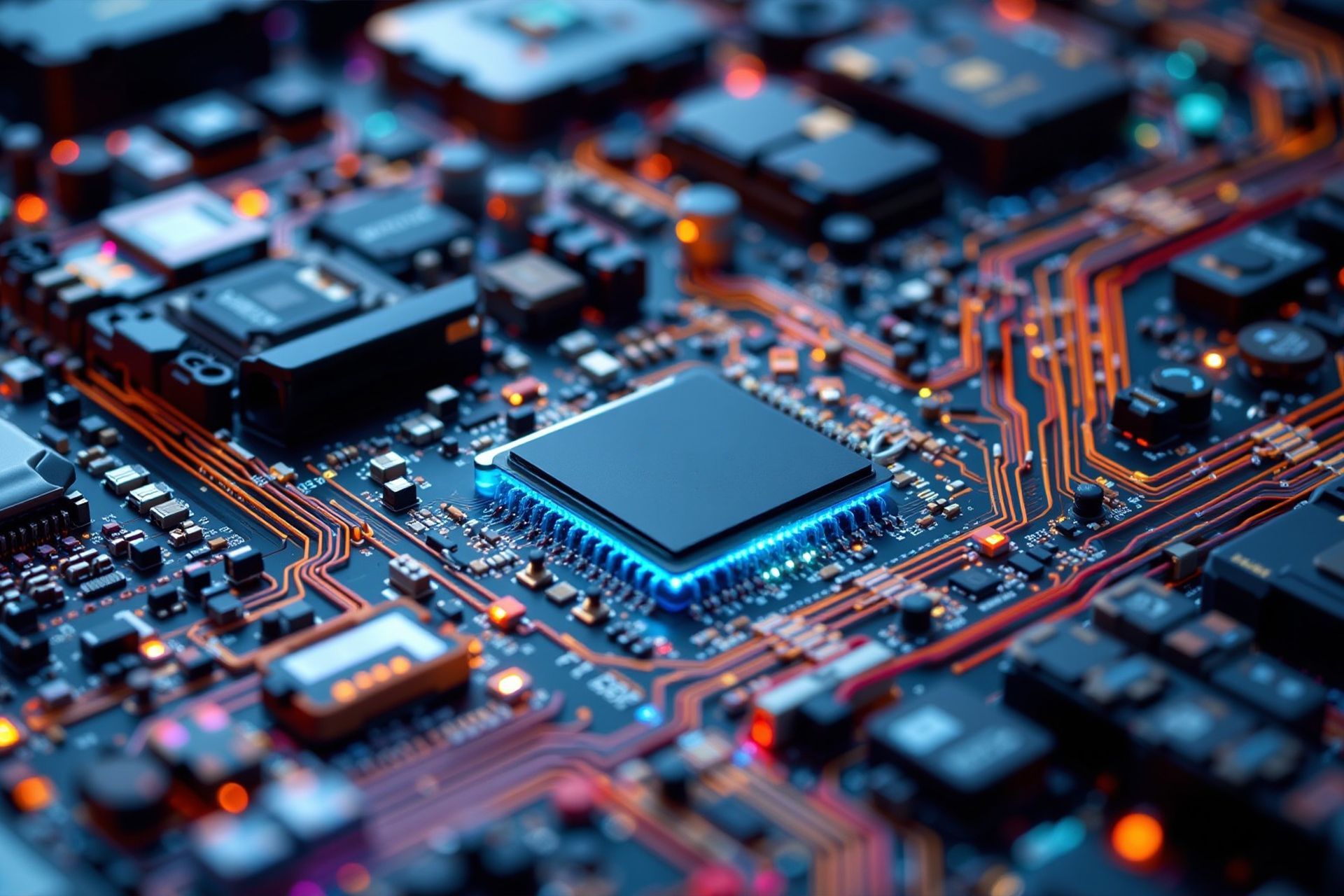
applications in Magnetic-Sensitive Environments
Aluminum is used extensively in industries that require minimal magnetic interference:
- Particle Physics: In electron/proton beamlines and accelerators, magnetic fields can deflect charged particle beams. Non-magnetic chambers help maintain beam stability and precision.
- Quantum Physics: Experiments like electric dipole moment (EDM) measurements or searches for new fundamental particles require extreme magnetic shielding and non-magnetic environments.
- Precision Metrology and Calibration: Instruments like atom interferometers, laser gyroscopes, and gravitational wave sensors operate in vacuum and are extremely sensitive to magnetic disturbances. Space-bound sensors in satellites, especially magnetometers, are often tested in vacuum. A non-magnetic environment ensures accurate calibration.
- Semiconductor Manufacturing: Because the circuits are drawn by an electron beam, which is easily influenced by magnetics, a non-magnetic vacuum environment is critical. Aluminum chambers are also used during production of diamond crystal wafers.
- Medical Equipment: Magnetic Resonance Imaging (MRI) and Nuclear Magnetic Resonance (NMR) machines and other imaging devices benefit from aluminum’s low interaction with magnetic fields
References:
Outgassing Properties of Various Surface Finished Aluminum: Alloy Measured by Extremely High Vacuum System - This paper shows the ultimate vapor pressure of aluminum to be: 7.5×10−16 Torr L s-1 cm−2. ≈ 10−12 Pa m3 s−1 m−2. https://www.researchgate.net/publication/354509096_Outgassing_Properties_of_Various_Surface_Finished_Aluminum_Alloy_Measured_by_Extremely_High_Vacuum_SystemOutgassing_Properties_of_Various_Surface_Finished_Aluminum_Alloy_Measured_by_Extremely_High_Vac
Hydrogen Solubility in Stainless Steels - Detailed studies have documented the hydrogen uptake in austenitic stainless steels, emphasizing the need for high-temperature degassing to remove absorbed hydrogen.
https://link.springer.com/article/10.1007/s11661-008-9506-5
Hydrogen Solubility in Aluminum - Data on hydrogen solubility in aluminum shows extremely low levels in the solid state, which contributes to its excellent outgassing properties.
https://www.alalloycasting.com/hydrogen-solubility-in-pure-aluminum/
Request the full list of references at info@atlasuhv.com
HOW CAN WE ASSIST IN YOUR PRODUCT DEVELOPMENT NEEDS?
From our first custom aluminum vacuum chamber, to our recent niobium to stainless steel fittings for satellite delivery rockets, to our standard bimetal and titanium flanges and fittings, Atlas Technologies has been the solution of choice for mission critical projects around the world. Whether you have a rough sketch, a full-fledged design, or just need a handful of our US-manufactured bimetal products, we can help.